B.I.G. is on a path to zero environmental footprint by 2030. That’s right, zero. To make this journey more tangible, we’d like to offer you a passenger’s seat from which you get immersed in our diverse sustainability projects. Every two weeks, we’ll share a new project. In this edition: Turfgrass turns waste into artificial grass.
One of our sustainability objectives is to become a landfill-free industrial group. To achieve this, we have various strategies. On the one hand, we try to drastically reduce the amount of waste our facilities generate. On the other hand, we aim to reuse or recycle all the remaining waste – either internally or with partners. A telling example of the way we reuse waste internally is Recyarn, a project via which we are taking a big step towards greener artificial grass.
Meeting renewed consumer demand
“What’s the word that always sticks when you hear the term ‘artificial grass garden’?”, asks Nuria Villena Lerin, R&D Manager at Turfgrass. “Indeed, artificial. People nowadays have a greater environmental awareness and some try to steer clear of artificial products whenever possible. But we prove that sustainable and artificial don’t have to be mutually exclusive. In short, we came up with a solution to integrate recycled content from external and internal waste streams into artificial grass production."
A 3-step approach
“Together with internal and external partners, Turfgrass went all in for Recyarn. First, we made a business case, including risks, investment requirements and potential recycling partners. Then, we conducted extensive research into types of polymers, pre-treatment, additives, the extrusion process, etc. to create a process handbook. On top of that, we reviewed the life-cycle analyses of artificial grass to measure progress. The first results of this 3-step approach are promising: we successfully integrated 5% waste content, coming 100% from our internal waste material, in our monofilaments fibres.
Closing the loop
“Although 5% might seem like a small share, it’s a first step on our route to make this product fully circular. But we wouldn’t be B.I.G. if we contented ourselves with this achievement. We now aim to raise the bar to 10% with the current recycled material and intend to go even further with new recycled material streams. Moreover, re-using waste means we’ll use less virgin raw materials for artificial grass – a first step in making artificial grass a circular product.”
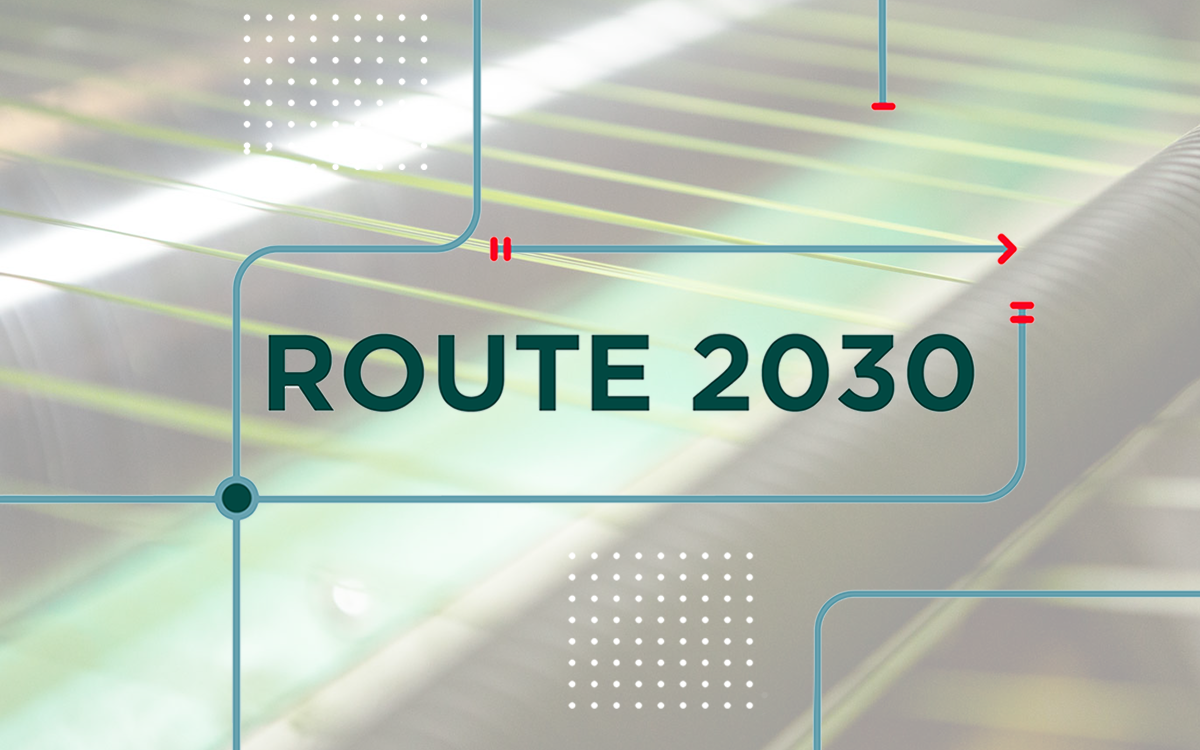